Would you have guessed? The start of every transit time measurement is in the lettershop
A floor occupied with mail of all kinds, three Spectos colleagues working next to a large printing machine. They are stuffing letters into envelopes. I am sitting in front of about two thousand transponders, all neatly stacked and sorted in large boxes. On my previous shift I had to check batteries for exactly these two thousand transponders. Each one with its own battery, which had to be tested for function and charge status. Affixing stamps and inserting address forms were also part of my assignments. But for what? Exactly, for those two thousand transponders from the previous shift. Between my A-levels and my studies, I worked for some time at the Spectos lettershop. While working on all these different tasks, a question kept coming to my mind:
What’s the purpose of cumbersome transponder sorting and affixing of stamps?
Back then, during the hours checking transponders, a big question mark hovered over my head. By now, I know what all these process steps were good for. Every transit time measurement starts in the Spectos lettershop. The lettershop is responsible for all preparatory and production steps, from the in-house production of test items, be they letters, packages or parcels, to their dispatch. With the help of the test shipments, important data and information about shipping routes, delivery times and delivery quality are determined for the respective clients. The process of monitoring the quality of delivery performance is called transit time measurement. A transit time measurement begins when a test shipment is dispatched, either from the Spectos location or from a previously defined drop-off point. From there, the shipment is on its way to trained panel participants, selected from a pool of Mailagents for this study. These participants then document the arrival of the shipment. Sometimes they send test items themselves using predefined guidelines. Ultimately, all information about the shipment’s progress, from start to finish, appears in our Spectos Real-Time Performance Management™ platform.
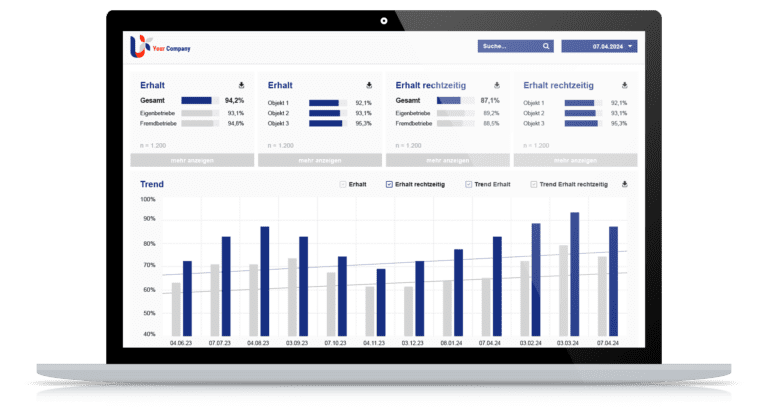
Sample view of the Post & Logistics Cockpit in our RTPM platform
First the work, then the pleasure!
It takes a lot of preparation before a test shipment can be dispatched. This brings us back to me and my two thousand transponders. Before the transponders are inserted into the mailings, quality checks have to be performed. We like to call this step ‘toasting’. As my main task at the time, I can now proudly claim to have toasted more than anyone else. The semi-active RFID transponders are tested one by one for their functionality. If necessary, the integrated battery must be changed – yes, for all those two thousand transponders, during each shift!
Small, but nonetheless important: What do our test shipments actually contain?
The transponders are equipped with RFID tags. When passing through readers, for example installed in the incoming and outgoing goods areas of sorting centers, the passive transmitters are detected both automatically and without contact.
Test mailings getting ‘married’ in our Lettershop
If live trackers are used for the measurements, they are also getting checked for proper functionality in the lettershop. In comparison to RFID tags, the live trackers transmit their position completely autonomously and thus capture the dispatch route from start to finish. On the shipments, the name and address of the client are displayed as the sender. This ensures that the lettershop mailings do not differ in any way from original ones. Depending on data needs and use case, the test items are either equipped with RFID transponders or with the Live Trackers. Our creative minds have named this process ‘marrying’. In the last phase, we feed the shipments into the shipping chain, as requested by the client. Now the test deliveries begin their journey to the recipients. All data on the current status of the shipments can be viewed by our clients in the Real-Time Performance Management™ platform.
Long story, great opportunities for postal service providers and bulk mailers!
I have now described the preparation of test mailings in the lettershop and the process of such a measurement. But why even conduct a transit time measurement, and why with us? Spectos is the number one address for companies that want to measure and optimize their quality of service and delivery. Knowledge about the duration and delivery quality of all kinds of shipments, whether they be letters, advertising mail or parcels, is extremely important. It can be used to improve customer satisfaction, to check compliance with SLAs or as proof of quality for tenders. This complex and normally very complex process, from the production of test shipments, to the selection and training of study participants to valid measurement results, is entirely managed by our solution for transit time measurements. The benefits at a glance:
The journey is the destination: well over two thousand transponders and glued envelopes later, I am now here, as a member of the marketing team, to give you an insight into our lettershop. It is the foundation and the beginning of our transit time measurements. Ultimately, every successful improvement in service quality begins on this mail-filled floor.
Did my look behind the scenes of the Spectos lettershop catch your interest in our transit time measurements?
Stay up-to-date on postal trends with our LinkedIn Channel for Postal & Logistics!